5 Satisfactry Tips

Implementing the 5 S methodology, also known as the 5 Satisfactory Tips, is a crucial step in improving the efficiency and productivity of any organization. This Japanese management technique focuses on maintaining a well-organized and standardized workspace, which in turn helps to reduce waste, improve quality, and enhance employee morale. The 5 S's stand for Sort, Set in Order, Shine, Standardize, and Sustain, each representing a vital aspect of this methodology.
Introduction to the 5 Satisfactory Tips

The 5 S methodology has its roots in Japan, where it was first implemented in the manufacturing sector to improve workflow and reduce inefficiencies. Over time, its application has expanded to various industries and sectors worldwide, including healthcare, education, and service industries. The core idea behind the 5 S’s is to create a work environment that is clean, organized, and safe, thereby fostering a culture of continuous improvement and employee engagement.
Key Points
- Sort: Remove unnecessary items from the workspace to reduce clutter and improve focus.
- Set in Order: Organize necessary items in a logical and accessible manner to improve efficiency.
- Shine: Clean and maintain the workspace regularly to prevent dirt and debris buildup.
- Standardize: Establish standards for organization and cleanliness to ensure consistency across the organization.
- Sustain: Make the 5 S practices a part of the daily routine to maintain the improved environment.
Breaking Down the 5 Satisfactory Tips
Each of the 5 S’s plays a critical role in achieving a well-organized and efficient work environment. By understanding and implementing these principles, organizations can significantly reduce waste, improve productivity, and enhance the overall quality of their operations.
5 S Element | Description |
---|---|
Sort (Seiri) | Separate essential from non-essential items and dispose of or store the latter appropriately. |
Set in Order (Seiton) | Organize necessary items in a way that they are easily accessible and clearly labeled. |
Shine (Seiso) | Clean the workspace regularly to maintain a high level of cleanliness and organization. |
Standardize (Seiketsu) | Establish standards for organization and maintenance to ensure consistency across all areas. |
Sustain (Shitsuke) | Make the 5 S practices a habitual part of the daily routine to maintain the improved work environment. |
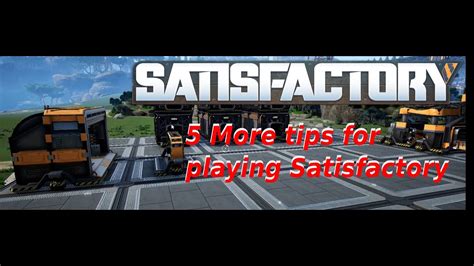
Benefits of Implementing the 5 Satisfactory Tips

The benefits of implementing the 5 S methodology are multifaceted. By reducing clutter and improving organization, organizations can significantly reduce the time spent searching for tools or information, thereby improving productivity. Additionally, a clean and well-maintained workspace contributes to a safer working environment, reducing the risk of accidents and injuries. The 5 S also fosters a culture of continuous improvement, encouraging employees to identify areas for improvement and suggest solutions.
Case Studies and Examples
Several organizations have successfully implemented the 5 S methodology, achieving significant improvements in efficiency, quality, and employee morale. For instance, a manufacturing plant in Japan reported a 30% reduction in production time and a 25% decrease in defects after implementing the 5 S. Similarly, a hospital in the United States improved patient satisfaction ratings by 20% after applying the 5 S principles to its operational processes.
What are the primary challenges in implementing the 5 S methodology?
+The primary challenges include resistance to change from employees, lack of leadership commitment, and difficulty in sustaining the practices over time. Addressing these challenges requires strong communication, training, and the establishment of clear goals and objectives.
How can the 5 S methodology be adapted to different industries and sectors?
+The adaptation of the 5 S methodology to different industries involves understanding the specific needs and challenges of each sector. For example, in healthcare, the focus might be on patient safety and infection control, while in education, it could be on creating an organized and conducive learning environment.
In conclusion, the 5 Satisfactory Tips offer a powerful framework for organizations seeking to improve their operations, reduce waste, and enhance employee engagement. By implementing these principles, businesses can achieve significant improvements in efficiency, quality, and productivity, ultimately contributing to their long-term success and sustainability.