5 Satisfactory Tips
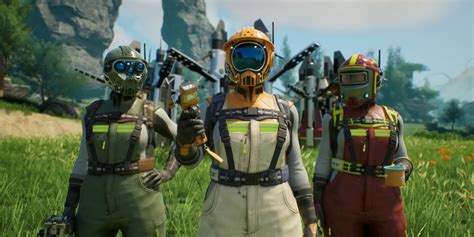
Implementing the 5 S methodology, a Japanese approach to organizing and managing spaces, can significantly improve productivity and efficiency in various settings. The term "5 S" stands for five Japanese words: Seiri, Seiton, Seiso, Seiketsu, and Shitsuke. Each word represents a step towards achieving a more organized, efficient, and effective work environment. This methodology has been widely adopted across different industries and cultures due to its simplicity and effectiveness.
Understanding the 5 S Methodology

The 5 S methodology is based on the idea that a well-organized workspace is more productive, safer, and easier to manage. By applying the principles of 5 S, organizations can reduce waste, improve quality, and enhance their overall performance. Here’s a breakdown of what each “S” represents:
Seiri: Sorting and Purging
The first step in the 5 S process is Seiri, which involves sorting and purging unnecessary items from the workspace. This includes getting rid of any obsolete, broken, or unused tools, equipment, and supplies. The goal is to eliminate anything that does not contribute to the work process or add value. By doing so, organizations can reduce clutter, minimize waste, and improve the overall efficiency of their operations.
Seiton: Organizing and Arranging
Once the unnecessary items have been removed, the next step is Seiton, which involves organizing and arranging the remaining items in a logical and accessible manner. This includes designating a specific place for each item, labeling storage areas, and implementing a system for maintaining organization. A well-organized workspace helps to reduce search times, improve workflow, and enhance employee productivity.
Seiso: Cleaning and Inspecting
The third step in the 5 S process is Seiso, which focuses on cleaning and inspecting the workspace. This includes regular cleaning of equipment, tools, and work areas to prevent the accumulation of dirt, dust, and other contaminants. Inspection is also a critical component of Seiso, as it helps to identify potential problems or hazards before they become major issues. A clean and well-maintained workspace not only improves safety but also reduces downtime and extends the lifespan of equipment.
Seiketsu: Standardizing and Maintaining
Seiketsu is about standardizing and maintaining the improvements achieved through the first three steps. This involves establishing procedures and protocols for maintaining the organized, clean, and efficient workspace. It also includes training employees on the importance of 5 S and their role in sustaining it. By standardizing processes and maintaining a high level of organization, organizations can ensure that the benefits of 5 S are long-lasting.
Shitsuke: Sustaining and Disciplining
The final step in the 5 S methodology is Shitsuke, which emphasizes the importance of sustaining and disciplining the new habits and practices implemented through the 5 S process. This includes creating a culture of continuous improvement, where employees are encouraged to identify areas for improvement and suggest new ways of working. Discipline is also crucial, as it involves holding employees accountable for maintaining the high standards of organization and efficiency established through 5 S.
Key Points
- The 5 S methodology is a systematic approach to organizing and managing spaces, enhancing productivity and efficiency.
- Each "S" represents a critical step: Seiri (sorting and purging), Seiton (organizing and arranging), Seiso (cleaning and inspecting), Seiketsu (standardizing and maintaining), and Shitsuke (sustaining and disciplining).
- Implementing 5 S can lead to reduced waste, improved quality, and enhanced overall performance.
- A well-organized workspace is safer, easier to manage, and more conducive to productivity.
- Sustaining the 5 S culture requires continuous improvement efforts and discipline among all team members.
5 S Principle | Key Activities |
---|---|
Seiri | Sorting, purging unnecessary items |
Seiton | Organizing, arranging items logically |
Seiso | Cleaning, inspecting the workspace |
Seiketsu | Standardizing, maintaining improvements |
Shitsuke | Sustaining, disciplining new habits |

As organizations continue to evolve and grow, the importance of maintaining a well-organized and efficient workspace becomes increasingly critical. The 5 S methodology offers a practical and effective approach to achieving these goals, providing a framework for improvement that can be applied in a wide range of contexts. Whether in manufacturing, healthcare, or any other industry, the principles of 5 S can help to drive positive change and support long-term success.
What are the primary benefits of implementing the 5 S methodology?
+The primary benefits include reduced waste, improved quality, enhanced productivity, and a safer working environment. By organizing and standardizing processes, organizations can also reduce costs and improve customer satisfaction.
How can organizations ensure the long-term sustainability of 5 S improvements?
+Long-term sustainability can be achieved by incorporating 5 S into the organizational culture, providing ongoing training and support, and continuously monitoring and evaluating the effectiveness of 5 S practices. It’s also essential to recognize and reward employees for their contributions to maintaining a 5 S environment.
Can the 5 S methodology be applied in non-manufacturing settings?
+Yes, the 5 S methodology can be applied in various settings beyond manufacturing, including offices, hospitals, schools, and service industries. The principles of 5 S are universally applicable and can help any organization improve its efficiency, productivity, and overall performance.